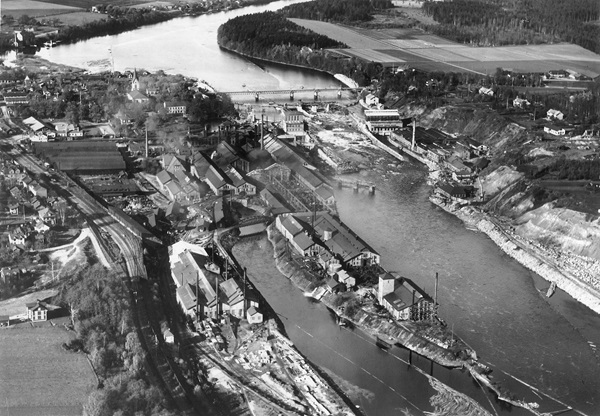
Early days: 1930s to 1970s
The very first stainless steels were pure austenite, ferrite, or martensite in the early 1900s. The first duplex grades, with a combination of ferritic and austenitic phases were developed in 1930 by the Avesta Ironworks in Sweden, which later became Outokumpu. The mill started selling the first two duplex grades to customers who needed to reduce intergranular corrosion, which can affect ferritic stainless steel.
In those early days, duplex grades were used to create castings, bar, and plate for the pulp and paper industry and elevated temperature applications thanks to their good corrosion resistance and castability. By 1932, they accounted for 6.5% of the total global stainless steel market of 5,500 tonnes.
Over the next few decades, metallurgists developed techniques to reduce the carbon level and introduce nitrogen to control the ductility and weldability. Shortages of nickel during the second world war prompted greater interest in duplex grades. Improvements in the 1950s included the development of grade that used nitrogen to reduce the likelihood of cracking during casting and welding.
Second generation of duplex
These developments culminated in the 1970s with the second generation of duplex grades, which found more applications and greater commercial success. These were better able to resist intergranular corrosion.
From a metallurgical perspective, these grades made use of increased nitrogen to enhance the formation of austenite. This prevents the duplex microstructure from reverting to full ferrite in the heat-affected zone after welding or hot working. Nitrogen also helped the materials to resist pitting corrosion and raised the strength level at the same time.
Super duplex grades
Developments in the 1970s and 1980s focused on higher compositions in the form of super duplex as the third generation of duplex grades. These grades contain more alloying elements and as a result have better properties but at a higher cost. They met demand from the offshore oil and gas, food and beverage and chemical processing industries.
The most common definition of a super duplex stainless steel is that it should achieve a Pitting Resistance Equivalent (PRE or PREN) of at least 40.
To achieve this level of corrosion resistance, metallurgists make use of alloying elements such as chromium, molybdenum, tungsten, nickel, and copper.
Of course, the higher amount of alloying elements in super duplex grades also means a higher cost, but they generally are very price competitive to the austenititc steels that may be considered alternatives.
Some companies have continued to extend highly alloyed grades by developing hyper duplex grades with PRE of almost 50. There are relatively few large-scale applications that presently call for this extremely high corrosion resistance level, so hyper duplex grades have not reached the mass market yet.
Lean duplex
At the other end of the scale, lean duplex grades were developed in the mid-1980s to minimize the cost of the raw materials.
This is particularly true when using nickel as an alloying element. The price of nickel has been particularly volatile over the years. Therefore, by reducing the nickel content, we have been able to offer customers price stability and more accurate business forecasting.
Of these lean grades, Forta LDX 2101 has been particularly popular. It has high manganese and nitrogen to compensate for its low nickel content. It provides high strength and good corrosion performance, and is still fully weldable.
Formable duplex
A further development during the last 10-15 years has been duplex steels with improved forming properties.
Until the development of formable duplex, other duplex grades did not have the right combination of ductility and high strength to create complex and lightweight formed components.