Tried and tested in extreme conditions
Outokumpu has been a key supplier of stainless steel to the oil and gas industry for more than 50 years. Our products can be found in upstream and downstream applications – from oil and gas production to transport and storage, refineries, LNG plants and petrochemical units. Tried and tested in these extreme conditions we have earned approvals from leading oil and gas companies worldwide.
We meet ASTM and EN standards, certification by bodies like Norsok, as well as customers’ own complex in-house specifications. These cover mechanical properties, length of coil and other dimensional standards.
One widely used standard for material certification is BSE EN 10204. It defines various levels for traceability and certification. We regularly supply to level 3.1, which requires testing at our own laboratory facility, as well as level 3.2, where an independent third party carries out certification.
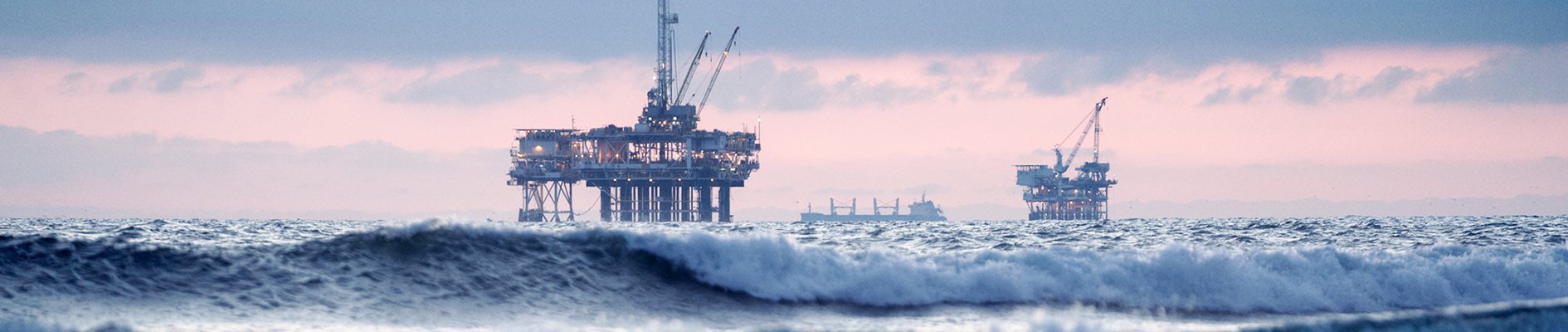
Corrosion resistant alloys
Depending on the application, our alloys may be competing with painted carbon steel at one end of the market and with nickel alloys at the other end. High levels of corrosion resistance ensure long life, process continuity and control of risk.
When high strength is also needed, duplex stainless steels such as Forta DX 2205, Forta LDX 2101 and Forta SDX 2507 are popular.
For extremely corrosive environments, alloys in our Ultra range are used widely. These include Ultra 825, a nickel alloy that can withstand sour environments and is therefore well suited to flowlines. In comparison, Ultra 904L, Ultra 254 SMO and Ultra 6XN are ideal for wet corrosion environments, with Ultra 254 SMO providing a cost advantage due to its high strength and relatively low nickel content.
Duplex allows lighter design
As wells are explored at greater depths, the piping becomes heavier. The superior mechanical strength of duplex stainless steel benefits the industry by allowing for lighter design. Outokumpu offers a wide range of duplex stainless steel grades, from lean duplex up to superduplex stainless steels.
Also on the platform, the increased mechanical strength of the duplex grades can be utilized. The present lifetime of a platform in stainless steel is more than 50 years with the intention to increase it even further. The technical challenges for the industry, such as increased depths, tar sands, heavy oils, more sour wells, arctic and high pressure / high temperature conditions require materials able to cope with these harsh environments.
Number one choice for sustainability
Sustainability is a major driving force in industry, with some energy companies setting an objective to achieve net zero operation by 2050 and others facing tightening regulation from governments. As a supplier of stainless steels and other alloys, we’re already ahead of the curve when it comes to carbon footprint. We have certified data in place so that our customers can calculate the carbon footprint of their own projects.
Our carbon footprint is 30 percent lower than the average. That’s partly due to our use of low-carbon electricity to power our mills and electric arc furnaces. Learn more about Outokumpu's take on sustainability