Crystal structure and microstructure
All steels are an alloy of iron and other carefully selected alloying elements. Pure iron exists normally in one of two main kinds of crystal structure: alpha-iron with a body- centered-cubic (bcc) lattice – forming a material known as ferrite, and a gamma-iron face-centered-cubic (fcc) lattice – forming austenite. When carbon (C) is present then a further crystal structure can be formed that results in another material – martensite, which has a body-centered tetragonal (bct) structure. This is important as martensite is very hard and is a significant factor in the strengthening of steel. However, rather than focusing on the atomic scale, we categorize a stainless steel according to the appearance of its ‘microstructure’, as examined using optical microscopy, typically at magnifications of 25x and above.Ferritic stainless steel
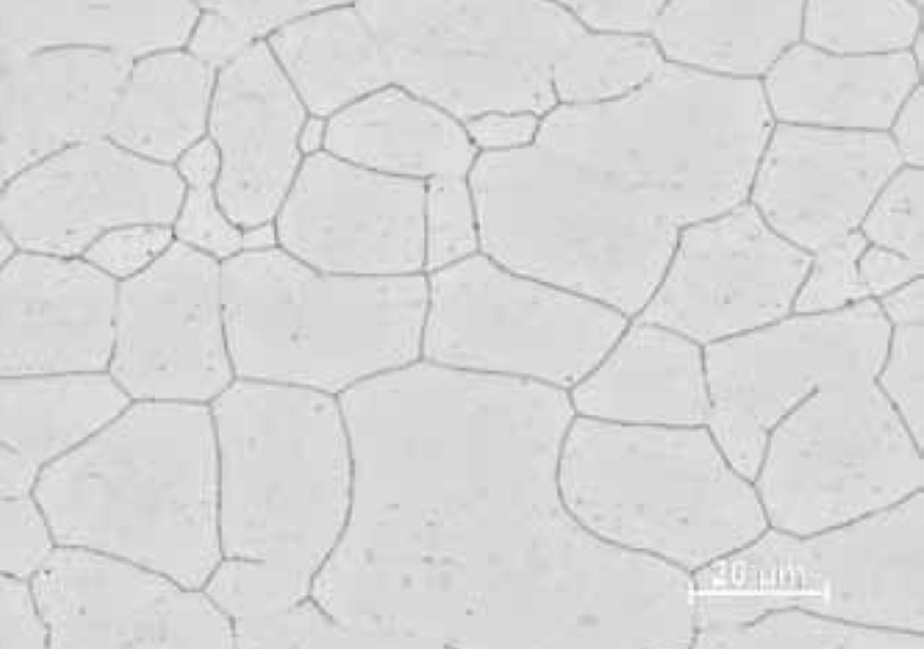
The standard ferritic grades, also known as Cr-steels, are alloyed with chromium (Cr) at 11.2–19%, but with no, or a very small addition of nickel (Ni). As nickel is one of the most expensive alloying elements and has historically demonstrated high price volatility, the low nickel content of the ferritic grades makes them more price stable compared to grades with high nickel content. Molybdenum (Mb) is added to some grades to improve the corrosion resistance, while alloying with niobium (Nb) and/or titanium (Ti) improves the weldability. Figure 1 shows a typical ferritic stainless steel microstructure. A key feature of ferritic steel is that it is magnetic. Typical applications are washing machines (see Figure 2), counter tops, refrigerators, dish-washers, cooker hoods, tableware and restaurant equipment, architectural use (mainly indoor), transport industry e.g. exhaust systems in automotive and structural hollow sections in heavy transport.
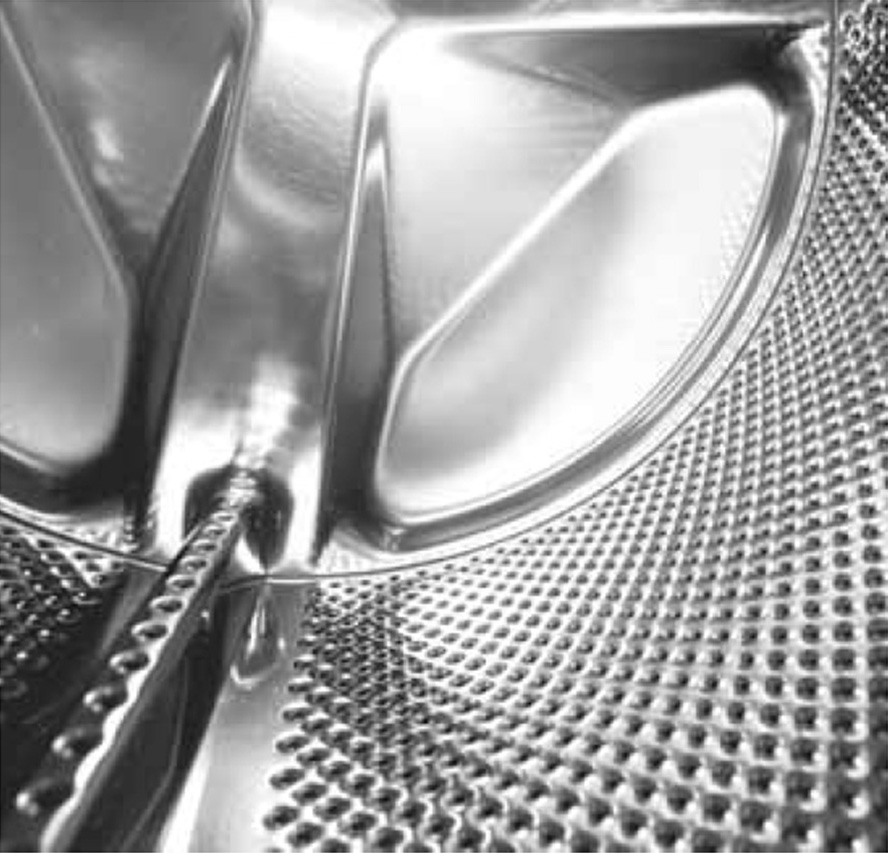
Ferritic high temperature grades
There are also high temperature ferritic grades with increased resistance to high temperatures (800–1150 °C). These are mainly used in applications with sulfurous atmospheres (as sulfur may react with nickel in austenitic grades) and/or at low tensile loads. These grades are typically alloyed with more carbon compared to standard ferritic grades, in order to increase the creep strength, and with silicon (Si) and aluminum (Al) to improve the resistance to oxidation.View Outokumpu ferritic stainless steel grades >
Martensitic and precipitation hardening stainless steel
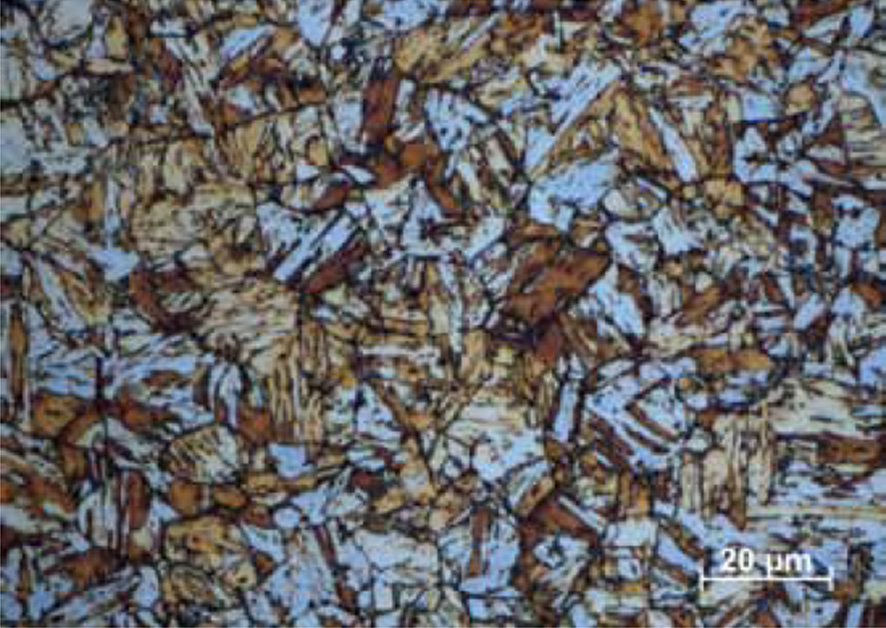
The martensitic grades (see Figure 3) are the smallest group of stainless steels. To improve their strength and hardenability they have a higher carbon content compared to other grades, and nitrogen (N)is sometimes added to further improve the strength. These grades contain no or rather small amounts of nickel, and molybdenum is seldom added. By adding some nickel and reducing the carbon content the rather poor weldability of martensitic grades can be improved. Sometimes sulfur is added to improve the machinability. The martensitic grades are magnetic and hardenable. The precipitation hardening grades are hardened by a special mechanism involving the formation of precipitates within the microstructure.
Martensitic grades are often used in applications where high strength and wear resistance is demanded, such as for shafts, knifes and for wear and press plates.
View Outokumpu martensitic and precipitation hardening stainless steel grades >
Austenitic stainless steel
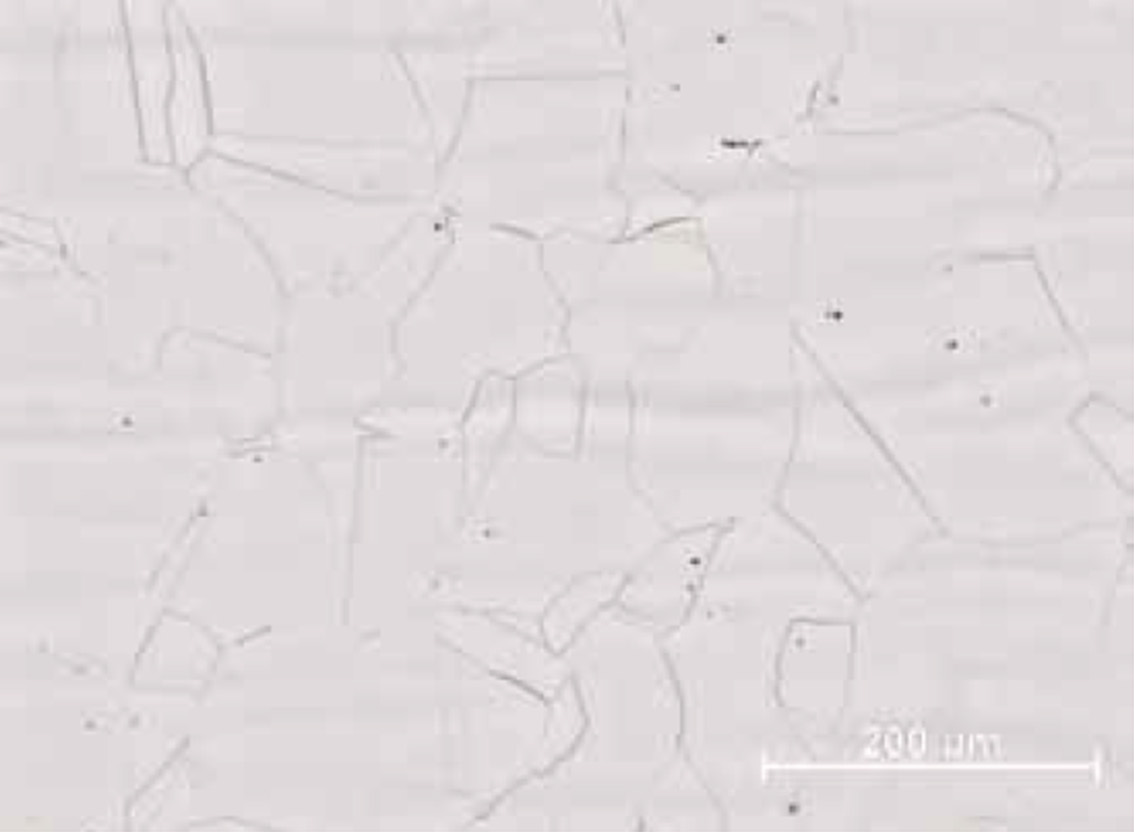
The austenitic grades (see Figure 4) are the largest group of stainless steels, and can be divided into five sub-groups:
- Cr-Mn grades
- Cr-Ni grades,
- Cr-Ni-Mo grades
- High performance austenitic grades
- High temperature austenitic grades
The austenitic grades have good to excellent corrosion resistance, good formability and weldability.
Their good impact strength at low temperatures is often exploited in cryogenic applications. The austenitic grades are non-magnetic in the solution annealed condition. Cold working increases their strength and certain grades are therefore supplied in the temper rolled condition and may then be magnetic due to the presence of some martensite. Typical applications for austenitic stainless steels are in the food industry, catering and kitchen equipment, process industries, building, architecture and transport.
Cr-Ni grades
The Cr-Ni grades are ‘general purpose grades” mainly alloyed with chromium and nickel, but with no molybdenum. These grades are sometimes referred to as 18-8 type of stainless steels, indicating the approximate chromium and nickel content. Some grades are alloyed with nitrogen to improve their strength, or with sulfhur to improve machinability. There are also stabilized grades where titanium or niobium is added to increase the mechanical properties at high temperatures by the formation of hardening carbides. Titanium and niobium stabilization was also used to avoid detrimental carbide precipitates on welding, but for modern low-carbon Cr-Ni steels this is not necessary.
Cr-Mn grades
In the Cr-Mn grades, also referred to as ‘200-series’ following the AISI/ASTM nomenclature, the nickel content is decreased and the austenitic microstructure is maintained by replacing some of the nickel with manganese and nitrogen. The chemical composition of grade 4372 is around 17% Cr, 4% Ni and 7% Mn. This grade has almost the same formability, corrosion resistance and weldability as grade 4301, but with higher strength.
Cr-Ni-Mo
These are also ‘general purpose grades’, but with increased corrosion resistance owing to alloying with molybdenum (2–3%), and they are sometimes referred to as ‘acid-proof’ stainless steels. The chromium content is around 17% and the nickel content 10–13%. Some grades are alloyed with nitrogen to improve the strength, or with sulfur to improve machinability. There are also stabilized grades where titanium or niobium is added to increase the mechanical properties at high temperatures by the formation of hardening carbides. Titanium and niobium stabilization was used to avoid detrimental carbide precipitates on welding, but in modern, low carbon Cr-Ni-Mo steels this is not necessary.
High performance austenitic
High performance austenitic stainless steels were developed for use in very demanding environments and have even higher alloying content. The chromium content varies between 17% and 25%, nickel between 14% and 25% and molybdenum between 3% and 7%. Many of these grades are also alloyed with nitrogen to further increase the corrosion resistance and strength. Some grades are alloyed with copper to increase their resistance to certain acids. The austenitic grades 254 SMO. and 4529 are sometimes referred to as 6Mo superaustenitic grades, and 654 SMO as a 7Mo superaustenitic grade.
High temperature austenitic grades
High temperature austenitic stainless steels are designed primarily for use at temperatures exceeding 550 °C which is in the temperature range where creep strength is the critical factor. The compositions of these steels are designed to provide a long service life in dry gases at high temperatures (800–1150 °C), with the focus on good oxidation resistance rather than resistance to aqueous corrosion.
The high temperature austenitic grades are characterized by high chromium (17–25%) and high nickel (8–20%) content but containing no molybdenum. Silicon is added in some grades to increase their oxidation resistance. Outokumpu’s MA grades are alloyed with silicon and also with cerium (Ce) to further increase their resistance to oxidation, and with nitrogen to improve the creep strength.
View Outokumpu austenitic stainless steel grades >
Duplex stainless steel
Duplex grades (see Figure 5) have a ferritic-austenitic microstructure, with a phase balance of approximately 50% ferrite and 50% austenite. Duplex grades combine many of the beneficial properties of ferritic and austenitic stainless steels. The duplex microstructure also contributes to a high strength and high resistance to stress corrosion cracking (SCC).
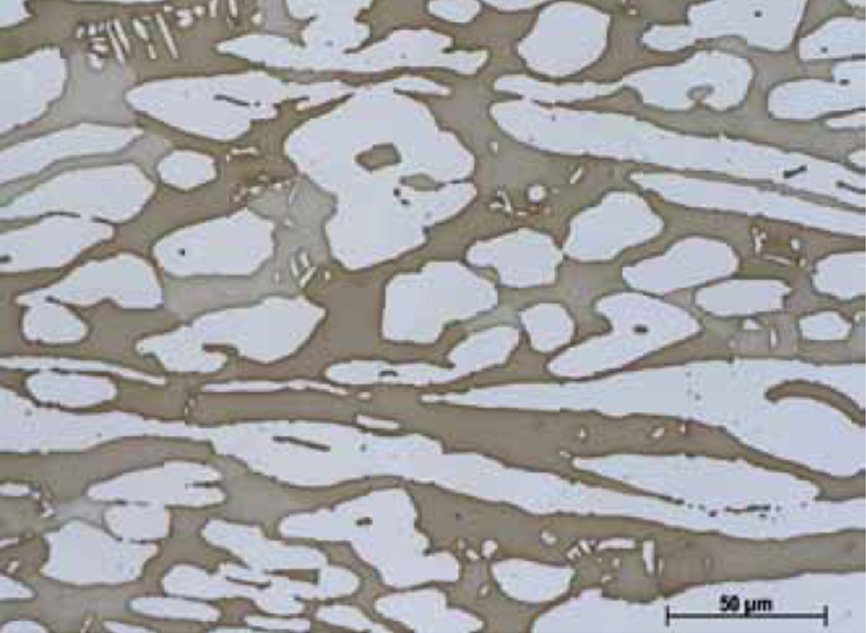
Typically, duplex stainless steels have a high chromium content (20.1– 25.4%) and a rather low nickel content (1.4–7%) compared to the austenitic grades. The low nickel content of the duplex grades makes them more price stable. Molybdenum (0.3–4%) and nitrogen are added to improve the corrosion resistance and balance the microstructure. Nitrogen also increases the strength.
Manganese is added to some grades, as partial replacement of nickel and also to increase the solubility of nitrogen in the material. The duplex grades LDX 2101 and 2304 are sometimes referred to as lean duplex grades. The duplex grade 2205 is sometimes referred to as 22Cr duplex and grades 2507 and 4501 as 25Cr superduplex grades.
The duplex grades are magnetic due to their ferrite content. Recently a new duplex grade with better formability has been introduced, this is Forta FDX 27.
Typical applications for duplex stainless steels are process industries, pulp & paper, oil & gas applications, desalination, chemical tankers (cargo tanks), pressure vessels and structural applications in harsh climates. Superduplex stainless steels are found in marine installations, oil & gas, flexible pipes, umbilicals and desalination plant.
Forta FDX 27 has excellent formability properties in comparison to other duplex stainless steels and close to standard austenitic stainless steels. It is ideal for the manufacturing of components with stretch forming as the primary forming operation such as heat exchanger plates.