Industrial operators have always been keen to minimize costs and invest in assets that provide value for money. But they are now also coming under growing pressure to reduce their carbon footprint.
Therefore, when investing in new storage tanks, it’s no surprise that many operators specify construction materials that represent the lowest lifecycle costs. This means that they take account of the full range of factors that represent cost throughout the entire lifecycle of the tanks.
These factors include material cost, welding, assembly and fabrication, delivery and logistics, local labor costs, application of internal and external surface treatment, inspection, repair and maintenance, as well as the scrap value of the tank walls at the end of its life. Over a lifetime, the initial purchase price of the raw material is only a fraction of the total lifecycle cost.
Many tank builders and owners find that selecting a high performance duplex grade of stainless steel is actually the lowest cost option over a lifetime. The duplex name is used because these grades combine the two most common phases of stainless steel (austenite and ferrite). This combination provides high strength, weldability and corrosion resistance that delivers high performance and long life.
High strength means less material is needed
Duplex stainless steel has high strength compared with other types of stainless steel. This is particularly helpful for storage tank designers as they can specify a tank with thinner walls.
This has three major benefits:
- Less raw material needed to build the tank
- More straightforward welding – the thinner the shell, the less time needs to be dedicated to welding the tank and less welding filler is needed.
- Lighter weight also means lower handling requirements and more
straightforward logistics for delivery to site
This graph shows how Outokumpu’s Forta range of duplex stainless steels (colored green) compare with common grades of austenitic stainless steel, carbon steel and mild steel.
Selecting a high performance duplex grade of stainless steel is actually the lowest cost option over a lifetime.
Weldability of duplex
Once on site, wider, longer and thinner plates will save time. Welding time (and cost) relates to the size of the tank and the shell thickness. Therefore, choosing large duplex stainless steel sheets will save time needed to prepare and weld joints.
Supporting this, we supply duplex stainless steel in sheets 2 meters wide as standard and up to 3.2 meters wide for special orders.
Duplex grades are not difficult to weld but do require a different approach to other types of stainless steel. It’s therefore important to follow our welding guidance carefully to use the correct welding parameters, joint configurations and fillers.
In practice, welding costs can vary widely between jobs. A skilled welder can cost 72 USD per hour in northern Europe but substantially less elsewhere. In addition, cost varies
depending on the grade of the steel – so it’s important to get an accurate local costing.
Once in operation, good weldability and fewer welds mean that a tank will have fewer potential points of failure. As a result, it will last longer and require less maintenance.
Corrosion resistance
For most tank builders, corrosion resistance is the single most important factor in ensuring that a tank has a long life. Duplex stainless steels have excellent corrosion resistance, so do not typically need protective coatings to store a wide array of products such as biodiesel, chemical feedstocks, marble slurry and other products.
In comparison, the coatings on carbon steel tanks need regular inspection and maintenance, which represent cost as well as the HSE risks of technicians working at height, sand blasting and chemical exposure.
- Internal environment – most tank builders specify the tank shell to withstand long exposure to the chemical that will be stored inside the tank. Choice of duplex grade will depend on the site specification.
- External environment – tanks in ports and marine sites that are exposed to elevated temperatures may be affected by stress corrosion cracking if not specified carefully. The microstructure of duplex stainless steel provides high resistance to stress corrosion cracking.
Eliminating the coating cuts the cost of initial application, as well as inspection, logistics, repair and lost availability of tanks. It also cuts out safety and environmental issues.
Price stability
Historic nickel price fluctuations
Twelve tanks for Acideka in Bilbao, Spain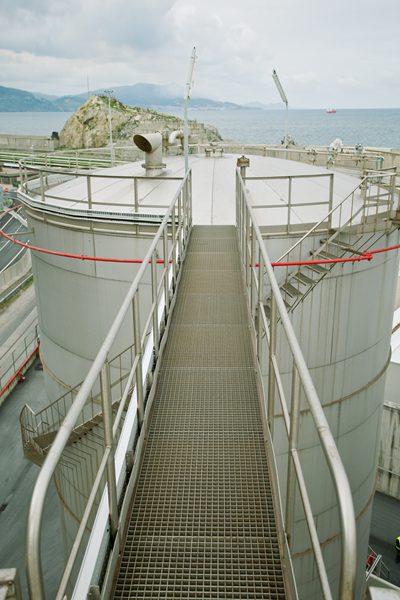
- Spanish chemical company Acideka ordered 12 new storage tanks for the Port of Bilbao, Spain, to store chemicals for water treatment, pulp and paper and other industries.
- Process equipment manufacturer De Dietrich Equipos Quimico originally requested a quote for 316L austenitic stainless steel
- Outokumpu suggested Forta DX 2304 duplex stainless steel in 2 meter plates as a cost-saving alternative.
- The result was 20 percent material savings, plus lower handling and welding costs
Minimizing welds for Gpi
- Process equipment firm Gpi won a contract for a 3,995 m3 tank (19 m diameter and 18 m high) to store demineralized water for Dow Chemical at the Port of Rotterdam.
- Outokumpu delivered 65 tonnes of hot rolled Forta 2205 for good corrosion resistance, high strength and certification that the material was inspected by an independent third party.
- We delivered coils of stainless steel in tightly specified dimensions to minimize the number of welds.
Biogas plant in Germany
- Sixteen digester tanks in Konnern, Germany, form the heart of a WELtec BioPower biogas park that provides enough energy for 10,000 homes.
- Each tank is 6.3m high and 25m in diameter and must withstand the sulfur and ammonia compounds that are by-products of biogas production.
- By specifying duplex stainless steel, the operator has maximized availability of the digesters, which are challenging to restart after a process outage.
- Outokumpu supplied 1,500 tonnes of stainless steel, with the highstrength material minimizing the thickness of the tank walls.
Conclusions
It’s vital to think about the long term when designing a chemical storage tank. Using duplex stainless steel can ensure significant savings in the long term because:
- High strength enables a tank with thinner walls, saving materials and civil engineering
- Weldability ensures straightforward fabrication on site
- Corrosion resistance delivers a tank with a long and trouble-free life
- Minimal nickel and molybdenum in the alloy represents price stability – and straightforward project planning.